En fonderie, si la silice se présente comme le sable le plus employé parce qu’il est facile à trouver et peu onéreux, il peut être nécessaire d’en mobiliser d’autres pour répondre à différentes contraintes (fabrication de pièces volumineuses, notamment). Ainsi, on peut aussi faire appel à des sables naturels ou encore synthétiques, en fonction des exigences du cahier des charges.
La silice
Disponible en quantités importantes et offrant un niveau de qualité toujours très régulier, la silice, très économique, est le sable le plus répandu en fonderie. On parle de sable siliceux pour désigner cette matière incontournable dans plusieurs procédés tels que le moulage au ciment, le procédé Ashland ou encore le procédé Croning.
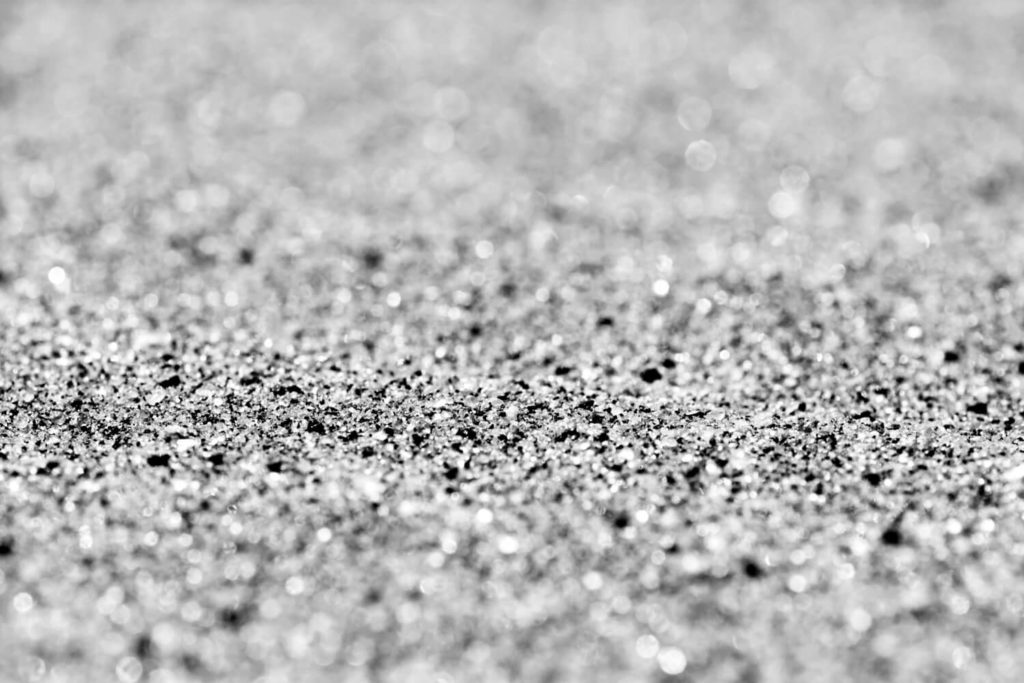
Les sables naturels
Après une préparation parfois matérialisée par des étapes de concassage, de tamisage ou encore de lavage. Les sables naturels peuvent être utilisés dans des cas spécifiques lors du moulage en sable. La chromite, par exemple, possède une température de fusion de 2 180° et se caractérise par des grains anguleux, avec une forme plus ou moins ronde selon les cas. Le zircon, quant à lui, peut être favorisé en raison de son caractère réfractaire : sa température de fusion est de 2 550°. On peut aussi choisir l’olivine, moins cher que la chromite et entrant également dans la catégorie des sables réfractaires non-siliceux. Enfin, on peut employer la kerphalite qui développe un degré élevé de mullitisation dès 1 300°.
Les sables synthétiques
En termes de prix, les sables synthétiques se placent assez souvent entre la chromite et le zircon. Assez rarement utilisés, ils sont toutefois employés dans quelques fonderies pour des pièces volumineuses en acier ou des zones fines de pièces automobiles. Généralement très résistants à l’agression du métal à haute température, ils sont frittés ou fondus au moment de leur usage.
Il faut savoir au moment de choisir un sable que celui-ci doit être réfractaire et résistant au choc thermique. Enfin, il doit montrer la dilatation thermique la plus faible possible, pour éviter que des zones de l’empreinte ne soient détruites.
Si vous avez besoin de conseils, n’hésitez pas à contacter un professionnel de la sous-traitance qui saura vous guider.